Workplace safety audit being integral part of safety management system is an important tool to identify gaps in existing procedures to real time implementation
We spoke to Ugandhar Phani Varma ASP, Managing Director, Center for Health Safety and Environment to understand the importance of a formal Occupational Safety Communication Program, the pre-requisites required to be followed by safety managers before they conduct a workplace safety audit and a key moment in his career where he wished he had handled a safety incident differently
Interviewed by Adeesh Sharma
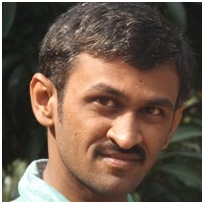
What are some of the key points that you would like to convey to employees as part of an Occupational Safety Communication Program?
Employees are key to successful implementation of safety program. Management shall design the program in a way where employees will take active part. Not all employees’ perspective of safety is the same; it depends on their experience, skill and previous organizational culture. While the responsibility of providing resources to ensure safety lies with employer, proper utilization of those resources would be the responsibility of employees.
Employees shall take upon themselves their safety and be observant of their surroundings while working. Negligence is not an option in workplace for them. Report all the hazards which are not addressed, incidents, near misses by which management can take prompt action to prevent major incidents. Never take decisions or take things for granted; if not sure ask your immediate supervisor. Respecting co-workers, preventing horseplays and ensuring proper housekeeping is part of employees job responsibility. Do the job for which you are trained for, never accept other tasks which does not come under your job responsibility. Safe workplace is your right; ask management for proper safety resources and work safely.
How would you address non-compliance to safety norms among employees?
Non compliances to safety norms by employees is a battling problem, that we commonly see in industrial and construction workers. In most of the organizations such problems are addressed by implementing fines. Though such procedures have produced results; Employees fear of being fined follow procedures, it is not an effective one in long run. There is always a sequence which can change culture; first train, train and train your employees. Make sure supervisor is capable enough to identify deviations in work procedures and correct them immediately. Make sure employees understand their responsibilities. Proper planning of job tasks will improve compliances. There is never a hurry to finish off the task, if planned well. Identify the gaps in existing procedures and implementation by which employee will not deviate. Compliment for their accomplishments; choose motivational programs which will not degrade the purpose of motivation. Be fair and treat all employees equally. Showing concern of employee well being has positive impact in culture and compliances. If nothing works then disciplinary action comes into play.
What are the pre-requisites for safety managers before they conduct a workplace safety audit?
Workplace safety audit being integral part of safety management system is an important tool to identify gaps in existing procedures to real time implementation; it gives us better opportunity to improve current system. In current practices safety audits are generally accompanied with checklists; which are easy to prepare and can be as detailed as required by the user. Prerequisites for a safety audit changes as per the organization, management system, process, experience of auditor and scope of audit. Before carrying out a safety audit, auditor shall prepare an exhaustive checklist which shall cover all range of activities including management system, documentation, workplace activities, legal compliances, etc. While carrying audit, audit team shall be equipped with few tools such as observation record sheet, camera (If allowed) and procedure to collect documentary evidence. Auditors shall have access to updated legal rules, acts and procedures. Nowadays, there are many software auditing tools which can be used to simplify the auditing process and reduce documentary part.
Please tell us about a key moment in your career where you wish you had handled a safety incident differently.
No one ever wants an incident to happen at a workplace, especially when you come from safety background. There was one incident which occurred under my safety supervision. Incident was dealt as per procedure, communication was perfect, injured party was sent to clinic after first aid and he was immediately transferred to hospital for medical treatment. Thanks to the injured party who was conscious and took right steps which helped us to perform better. We almost ate nothing the whole day taking care of injured party, doing investigation, preparing incident reports, witness reports and submitting it to client. End of the day I have realized the importance of being ready, though everything went right as per procedures there was lag, a certain amount of time which took us admitting the injured person in hospital and the state IP was in; no words would consol him. If the injury was critical, we would be helpless even after all the efforts we put in that day. We have identified the cause and it points to management commitment and preparedness. The delay was because the employee was not insured. It was not communicated by management to employees neither employees asked management about the insurance. Even though the employees were not insured, management shall take proper precautions for when such unexpected incidents happens, so that at least injured party would be admitted and treated without any delays. From then I educate safety professionals to look into employees insurance and suggest to at least tie up with nearby medical facility to provide immediate treatment.