Engaging employees in safety decision-making processes and soliciting their feedback can help foster a positive safety culture
3S LIFE SAFE AKADEMIE , India is a fast-growing, well-known, leading institute in "Occupational Health & Safety" with Courses Like NEBOSH, IOSH and "Diploma in Fire and Safety" and Diploma in Industrial Safety. They demonstrate the importance of safety and creating a safe work culture by means of successful training and workshop.Rahul Aren, (CertIOSH, IDipNEBOSH), HSE Manager and Trainer, 3S LIFE SAFE AKADEMIE, Bengaluru talks more about it.
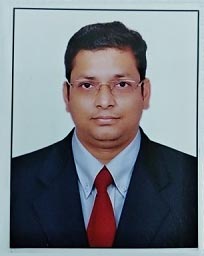
Interviewed by Adeesh Sharma
1. Please tell us about your organization and its focus areas in HSE.
3S LIFE SAFE AKADEMIE , India, a fast-growing, well-known, leading institute in “Occupational Health & Safety” Courses Like NEBOSH, IOSH and “Diploma in Fire and Safety” and Diploma in Industrial Safety.
We are demonstrating the importance of safety and creating a safe work culture by means of successful training and workshop. We are emphasizing that Safety should be the priority for everyone and everywhere. We are providing necessary safety training to various organizations across the country. Today, we have close to 1000 numbers clients as a corporate organization where we have successfully demonstrated our skills to improve safety awareness among organizational employees. We are committed create a safety culture and its importance in our society and various workplace.
3S LIFE SAFE AKADEMIE was founded in 2015 with the theme of “SAFETY”, “SECURITY” & “SURETY”. It’s an ISO 9001:2015 certified institute with International accreditation with NEBOSH, UK as a Gold Learning Partner no 1478 and National accreditation with NCVTE, Ministry of HRD, Govt. of India. In addition corporate member of IOSH, UK. no 4501.
The brand image and reputation of 3S LIFE SAFE AKADEMIE are encouraging having an average Google rating of 5 &Just dial rating of 4.7. Such an encouraging customer rating is only due to our ability to deliver and provide high-quality services to everyone.
2. What challenges do you face as a key HSE professional?
During our day-to-day business, we come across various business houses, industries, organizations, and professionals. The following challenges are mainly noticed.
Addressing these challenges requires a comprehensive approach that involves leadership commitment, employee involvement, ongoing training and communication, and a continuous improvement mindset towards safety culture.
- 1. Lack of Awareness or Training : Employees may not be adequately informed or trained about safety rules and procedures, leading to non-compliance or misunderstandings about safety protocols. The various level of management are not fully well versed in the main essence of Factories Act 1948, BOCW Act 1996 etc. These acts and rules are just considered legal compliances, and anyhow, these compliances are just fulfilled.
- 2. Resource Constraints : Limited resources, both financial and human, can impede safety implementation efforts. This may include insufficient Safety budget for safety equipment, inadequate staffing for safety training, or lack of time allocated to safety-related tasks. In India the few safety officers are hired even in the big projects and Indian legal requirement does not force to hire more Safety professional even the nature of work is high-risk. Safety budget is always a expenditure budget and it is understood that it is a sunk cost for the organisation. They are not familiar with the direct and indirect benefits of implementing the Health and safety at the organisation like Zero Lost Time Injury ( LTI) , Zero production downtime, No compensation cases , high level of productivity through safe workplace etc.
- 3. Resistance to Change : One of the most significant challenges is resistance from employees or management who may be resistant to changes in procedures or processes necessary for safety improvement. The organisation doing the work like Traditional Safety management (till the accident will not happen, everything is right ) . This resistance can stem from various factors such as complacency, fear of job loss, or simply discomfort with new ways of working. The Proactive safety management system to be implemented by the organisation to avoid any accident or incident.
- 4. Cultural Barriers : Organizational Safety culture plays a significant role in safety implementation. If there is a negative safety culture that prioritizes productivity over safety it can hinder effective safety measures. The presence of blame culture or toxic culture create negative atmosphere in the organisation and does not allow growth and implementation of the safety protocol.
- 5. Lack of effective Communication Issues : Poor communication can lead to misunderstandings or gaps in safety procedures. This includes unclear safety policies, ineffective dissemination of safety information, or language barriers in multilingual workplaces. The daily Tool Box Talk to be conducted and various verbal, written and graphic tool to be used for effective communication with all the workers or staf.
- 6. Inadequate Risk Assessment : Failure to accurately identify and assess potential hazards can result in ineffective safety measures. Without a thorough understanding of the risks involved, it's challenging to implement appropriate safety protocols.
- 7.Inconsistent Enforcement : Inconsistencies in enforcing safety policies can undermine their effectiveness. If there are no consequences for non-compliance or if enforcement is arbitrary, employees may not take safety protocols seriously.
- 8. Lack of Employee Engagement : Employees who are not actively involved in safety initiatives may not feel personally invested in maintaining a safe work environment. Workers are rarely consulted otherwise they are just informed. The experienced workers also never engaged while developing any Safe Operating Procedures (SOP) . Engaging employees in safety decision-making processes and soliciting their feedback can help foster a positive safety culture of safety ownership.
3. What strategies/solutions you deploy to alleviate those challenges?
Implementing health and safety measures in the workplace requires a multi-faceted approach that involves various strategies. Here are some possible strategies for effective implementation:
- 1. Leadership Commitment : Ensure that senior management demonstrates a strong commitment to health and safety. Leaders should visibly prioritize safety, allocate resources for safety initiatives, and actively participate in safety programs
- 2. Establish Clear Safety Policies and Safety Procedures : Develop and communicate clear and concise health and safety policies and procedures tailored to the specific needs and risks of the workplace. Ensure that all employees understand their roles and responsibilities regarding safety.
- 3. Employee Training and Education : Provide comprehensive safety training to employees on safety procedures, hazard recognition, and the proper use of safety equipment. Regular refresher training should be conducted to reinforce safety protocols and keep employees informed about any updates or changes.
- 4. Effective Risk Assessment and Hazard Identification : Conduct regular risk assessments to identify potential hazards in the workplace. Involve employees in the process of hazard identification to leverage their frontline knowledge and experience. Prioritize hazards based on their severity and likelihood of occurrence.
- 5. Implement Safety Controls : Implement appropriate safety controls to mitigate identified hazards. This may include engineering controls (e.g., machine guards), administrative controls (e.g., safety protocols), and personal protective equipment (PPE). Regularly review and update controls as needed.
- 6. Encourage Reporting and Participation : Establish a culture that encourages employees to report safety concerns, near misses, and incidents without fear of retaliation. Implement a system for reporting hazards and incidents and ensure that all reports are promptly investigated and addressed.
- 7. Safety Committee or Representatives : Establish a safety committee or designate safety representatives to oversee safety initiatives and serve as liaisons between management and employees. Involve representatives from different departments to ensure diverse perspectives.
- 8. Promote Positive Safety Culture : Foster a positive safety culture where safety is valued and integrated into everyday operations. Recognize and reward safe behaviors, involve employees in safety decision-making, and communicate regularly about safety achievements and goals.
- 9. Regular Safety Inspections and Audits : Conduct regular Safety inspections and audits to assess compliance with safety policies and identify areas for improvement. Address any deficiencies promptly and track progress over time.
- 10. Continuous Improvement : Implement a process for continuous improvement of health and safety performance. Regularly review safety data, solicit feedback from employees, benchmark against industry best practices, and make adjustments to safety programs as needed.
By adopting these strategies and fostering a proactive and collaborative approach to health and safety, organizations can create a safer work environment for their employees and reduce the risk of workplace injuries and incidents.
4. What are your views on current HSE scenario in Indian industries and what more needs to be done to change it?
In India, industries face several challenges when it comes to implementing health and safety measures. Some of the main problems include :
- 1. Lack of Awareness : There is often a lack of awareness among both employers and employees regarding health and safety regulations, standards, and best practices. Many small and medium-sized enterprises (SMEs) may not have the resources or expertise to develop comprehensive safety programs.
- 2. Poor Infrastructure : Some industries in India, particularly those in the informal sector or rural areas, may lack basic infrastructure such as proper ventilation, lighting, sanitation facilities, and emergency exits. This makes it difficult to ensure a safe working environment.
- 3. Limited Resources : Many industries, especially smaller ones, struggle with limited financial resources to invest in safety equipment, training programs, and infrastructure improvements. Cost considerations may lead to shortcuts or compromises in safety measures.
- 4. Inadequate Regulatory Enforcement : While India has regulations in place to ensure workplace safety, enforcement can be inconsistent, particularly in remote or rural areas. This lack of enforcement may lead to non-compliance by employers who prioritize cost-cutting over safety.
- 5. High Turnover and Informal Labor : Some industries in India, such as construction and manufacturing, rely heavily on informal labour, which may lack proper training and awareness of safety protocols. High turnover rates in these sectors can make it challenging to maintain consistent safety standards.
- 6. Cultural Attitudes : There may be cultural attitudes that prioritize productivity over safety, leading to resistance to safety measures or a lack of awareness about the importance of workplace safety. Additionally, hierarchical structures in some industries may discourage open communication about safety concerns.
- 7. Language and Literacy Barriers : In multilingual workplaces, language barriers can hinder effective communication of safety instructions and procedures. Additionally, low literacy rates among workers may make it difficult for them to understand written safety materials.
- 8. Inadequate Occupational Health Services : Access to occupational health services, including medical examinations and treatment for work-related injuries or illnesses, may be limited, particularly in rural areas. This can result in underreporting of workplace injuries and illnesses.
- 9. Supply Chain Challenges : In industries with complex supply chains, ensuring safety standards across all stages of production can be challenging. Subcontractors and suppliers may not adhere to the same safety standards, posing risks to workers throughout the supply chain.
Addressing these challenges requires a multi-stakeholder approach involving government agencies, industry associations, employers, workers' organizations, and civil society groups. Efforts to improve health and safety in Indian industries should focus on raising awareness, enhancing regulatory enforcement, providing resources and support to SMEs, improving infrastructure, and promoting a culture of safety and compliance.
5. What new HSE initiatives are you planning to implement within your organization in the near future?
Innovations in technology and evolving best practices continually shape the field of Health, Safety, and Environment (HSE). Here are some of the latest and advanced HSE initiatives that can be applied across various industries :
- 1. Digital Safety Management Systems : Implementing digital platforms and software solutions for managing safety data, incident reporting, risk assessments, and safety audits. These systems can streamline processes, improve data accuracy, and enable real-time monitoring of safety performance.
- 2. Internet of Things (IoT) for Safety Monitoring : Utilizing IoT devices such as wearables, sensors, and connected equipment to monitor environmental conditions, worker behavior, and equipment performance in real-time. IoT-enabled safety systems can detect potential hazards, alert workers to dangers, and prevent accidents before they occur.
- 3. Predictive Analytics for Risk Management : Employing predictive analytics tools to analyze historical safety data, identify trends, and predict future safety risks. This allows organizations to proactively address potential hazards and implement preventive measures to mitigate risks.
- 4. Virtual Reality (VR) and Augmented Reality (AR) for Training : Leveraging VR and AR technologies to create immersive and interactive training simulations for safety training and emergency preparedness. VR and AR-based training programs provide realistic scenarios that allow workers to practice safety procedures in a controlled environment.
- 5. Artificial Intelligence (AI) for Safety Insights : Using AI algorithms to analyze large volumes of safety data and identify patterns, correlations, and insights that may not be apparent through traditional methods. AI-powered safety analytics can help organizations make data-driven decisions and prioritize safety interventions.
- 6. Behavior-Based Safety (BBS) Programs : Implementing behavior-based safety programs that focus on understanding and modifying human behavior to improve safety outcomes. BBS initiatives involve observing and analyzing worker behavior, providing feedback, and implementing interventions to promote safe practices.
- 7. Remote Monitoring and Telepresence : Employing remote monitoring technologies and telepresence solutions to oversee operations in hazardous or remote environments without exposing workers to risk. Remote monitoring allows for real-time supervision, troubleshooting, and decision-making from a safe location.
- 8. Psychological Health and Well-being Programs : Recognizing the importance of mental health in workplace safety and implementing programs to support employee well-being. This includes providing access to counseling services, promoting work-life balance, and raising awareness about mental health issues.
- 9. By embracing these advanced HSE initiatives organizations can enhance their safety performance, protect their workers, and create healthier and more sustainable workplaces. It's essential to continually evaluate emerging technologies and best practices to stay ahead of evolving safety challenges.