Hazop Risk Assessment and Management in Industries
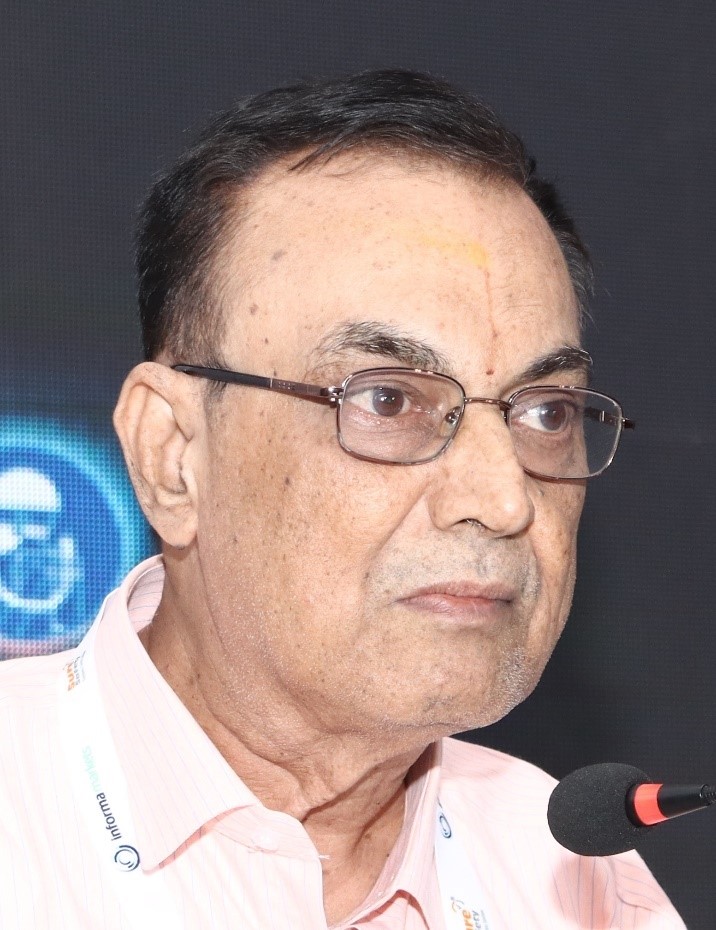
HAZOP is a structured and systematic examination of complex placement of process or operation to identify and evaluate problems that may represent risk to personnel or equipment. The intention of preparing is to review the design to pick up design or otherwise engineering issues that have not been considered. The technique is based on overall complex design within a number of simple sections called nodes, which are then individually reviewed. It is carried out by a multidisciplinary team (HAZOP) during a series of meetings. The HAZOP technique is quantitative and aims to stimulate the inspiration of the participants to identify the potential hazards and operating problems. Structure direction is given to the review process by applying standard guide word prompts to the review of each node. The relevant international standard calls for team members to display instruction and good judgment and for the meetings to be held in an interior climate of positive thinking and frank discussion. HAZOP is used in nuclear power plants, software development, and batch operations.
Method
The method applies to complex processes for which design information is available. For process plants, nodes are chosen so that each meaningful design intent can be specified, and they are commonly indicated on piping instrumentation diagrams and process flow diagrams. For each node in turn, the HAZOP team uses a list of standardized guide words and process parameters to identify potential deviations from design intent. For each deviation, the team identifies possible causes and likely consequences, then decides whether an action to instill an additional safeguard is necessary to reduce the risk to an acceptable level.
Guide Words
In order to identify deviations, the team applies (systematically in order) a set of guide words to each node in the process. Consider appropriate parameters that apply to the design intent. These are general words such as flow, pressure, temperature, and composition.
Objectives of HAZOP Study
HAZOP in the process industry may be focused either on the assessment of safety (with a consideration of possible risk for both equipment and operators) or on the operation (with regard to maintaining the required quantity of the product).
- Possibility of deceleration/decomposition of raw materials.
- Possibility of a failure of human factors.
- Possibility of an exothermic reaction.
Decomposition of Hazard from Raw Material, Reaction Mixture, Inter-meetings, and Final Product
- Possibility of an undesired reaction.
- Possibility of utility failure.
Advantages of HAZOP
- Systematic and thorough examination of the process equipment with an aim to identify potential issues.
- Possibility to evaluate the consequences of a failure involving personnel and study dangerous situations.
- Identification of new dangerous situations through a systematic procedure.
- Improved operational efficiency by identifying situations that may disrupt planned operations, damage equipment, or lead to unprocessed raw material loss.
- Better understanding of the process, even experienced members of the process of the meeting acknowledge a new dimension new,Information recording the operation of the assessed equipment.
Disadvantages
- Long time needed (depends on the size of the backlog).
- Need to clarify the objective/focus and setup of HAZOP studies at the beginning of the study.
- High demands on the knowledge and skills of the participants; without a good HAZOP team and leader, the process cannot be done effectively.
Risk Management and Assessment
Risk management can be defined as the collection of culture, process structures that are directed towards realizing potential opportunities while managing adverse effects. It can be described as a systematic application of management policies, procedures, and practices. Risk management also incorporates several other tasks such as identifying, analyzing, evaluating, monitoring, and reviewing risk.
Risk assessment is carried out using methods, tools, and risk assessment schemes. This involves identifying strengths and weaknesses in the approach and recording results through fault trees, event trees, and spreadsheets.
Event tree schemes are focused on a determined chain of events, while spreadsheet methods address the full scope of risk assessment (identification, analysis, and evaluation).
Background Knowledge
Risk assessment is part of a broader risk management program aimed at controlling risks and preventing accidents. Safety management should be both reactive and proactive. Risk management usually involves four stages: identification, analysis, evaluation, and mitigation.
Quantitative Risk Analysis
Using qualitative evaluation of all identified scenarios allows the contractor to focus on major technological issues, propose appropriate technical/organizational recommendations to minimize risks, and implement the recommendations.
Using a quantitative method:
R = P * S
- P is the probability of occurrence.
- S is the severity of the occurrence.
Qualitative Risk Analysis
Qualitative risk analysis is based on brainstorming to develop scenarios and identify safety functions through creative exploration of deviations.
HAZOP Study for Quantitative Risk
Traditionally, HAZOP studies and process hazard analysis (PHA) are held separately, producing two distinct databases. The HAZOP technique is grounded in applying guide words (e.g., more, less) to each process variable (e.g., temperature, flow, pressure). PHA, on the other hand, allows for defining risk positions to prioritize using frequency and severity categories as risk values.
Quantitative Approach of HAZOP
The aim is for integration with the risk matrix. This method incorporates the use of HAZOP and diagnostic methods, including parameters, guide words, and deviations for each node. From that, causes and consequences related to deviations are investigated.
From the HAZOP spreadsheet:
- Guide word/Deviation/Cause/Consequence.
PHA tool:
- Frequency/Severity/Risk/Mitigation.