Understanding Health Risks and Hazards in Laboratories
Working in a laboratory environment requires constant care, attention, and diligence. Every environment like this comes with a wide range of inherent risks and hazards, from open flames and dangerous chemicals to precarious electrical equipment and combustible elements, all of which need to be properly identified, assessed, and controlled.
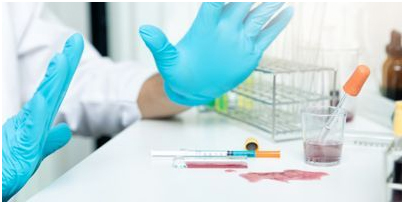
Laboratories are essential spaces for scientific analysis, intricate experiments, and controlled reviews, which means that any potential dangers cannot be overlooked, however minuscule they may be. When all the various risks are not controlled or handled in a safe, compliant, and approved manner, the potential side effects and health problems that arise can range from acute and temporary to chronic and life-threatening.
Managers of laboratories or biomedical facilities where careful research and analysis are key must maintain a proactive – rather than a reactive – approach when addressing health and safety risks in these environments.
This guide breaks down some of the most noteworthy health risks and hazards found in UK laboratories, and how to mitigate them to preserve workplace and worker safety.
Types of Health Risks and How to Overcome Them
Chemical Hazards
Exposure to hazardous chemicals can occur through inhalation, skin contact, ingestion, or injection. Chemical hazards can cause acute conditions like burns, irritations, dizziness or, on the worse end of the spectrum, chronic issues like organ damage. Long-term exposure to hazardous chemicals without proper protection can also increase the chances of serious illness.
Mitigation strategies involve proper usage of personal protective equipment (PPE), including gloves, goggles, face shields, lab coats and biohazard suits, in extreme cases. Labelling of chemicals and review of Safety Data Sheets is also critical, as is the disclosure of all potential side effects of improper use of intricate diagnostics equipment, for use outside of a controlled lab facility.
Physical Hazards
Improper use of lab equipment and tools can result in physical injuries such as cuts, lacerations, electric shocks, trips, and burns, to name just a few. Falls due to slippery surfaces or obstructed walkways also need to be prevented as much as possible.
Careful handling of equipment, testing and tagging of faulty electrical tools, cleaning spills promptly, and keeping walkways obstruction-free are some prevention methods. Clear signage and signposting are also practical ways to address any seemingly innocuous risks, particularly in crowded laboratories and facilities.
Biological Hazards
Working with infectious agents like microbes, bacteria, viruses, fungi or biological tissues and fluids brings the risk of contamination and disease transmission via inhalation or accidental inoculation. Contamination of elements, however small, can mandate the need for immediate prevention and containment.
Consult relevant COSHH biosafety regulations material for clear procedures and prevention steps should any chemicals or elements unexpectedly combine. Using the correct safety cabinets and testing equipment, and disposing of contaminated biological waste in the designated bins are also essential.
Fires and Explosions
Flammable chemicals, open flames from bunsen burners or heating equipment, faulty electrical gear or overloaded sockets increase the chances of burns and scalds to personnel. On a larger scale, should combustible materials combine, it could lead to dangerous explosions.
Proper storage of flammable materials – away from naked flames – is crucial. Storing them separately from less dangerous materials is a great way to protect lab technicians from experiencing fire unexpectedly. Correct training of fire extinguishers and blankets also helps to lower risks.
Minimising Air Contaminants
Fumes discharged from chemicals or equipment and particulate matter in the air commonly lead to breathing issues or allergies when inhaled. While some fumes may only cause minor, acute irritation, constant exposure can have long-term effects if not properly addressed.
Proper ventilation of facilities is vital to ensure that monoxide gases can escape without harming personnel. Air quality monitoring along with sufficient PPE for all technicians will also help to minimise the risks of dangerous chemical inhalation.
Avoiding Noise Issues
While minimal on the surface, constant exposure to high levels of noise – emitting from equipment like centrifuges, washers, mechanics, and machinery – all have a knock-on effect on health and well-being. Noise pollution is directly linked to fatigue, poor concentration, and if technicians do not take adequate precautions to safeguard hearing.
Placing overly noisy equipment in isolated rooms and mandating the use of earplugs are both essential to protecting personnel. Regular inspection and testing of machinery and equipment, and ensuring they are kept in good working order are also excellent, proactive ways to alleviate long-term hearing risks.
Ergonomic Strains
Long hours working while standing upright, or in awkward postures at lab benches and workstations, can lead to musculoskeletal damage. Improper handling of equipment can also cause serious injuries and issues, particularly if the objects are heavy and awkward to manoeuvre.
Proper provision of ergonomically friendly furniture and moving equipment will help workers avoid more musculoskeletal injuries and damage. Administering frequent breaks and rotations to avoid constant damage will also help minimise the level of ergonomic strain placed on each facility technician.
Lab Safety Provisions in Line with HSE Recommendations
Having adequate first aid equipment and other health provisions like cleaning kits, PPE, and safety signage will all help to prevent the problems listed above. Deploying clear and regular washing and cleaning schedules to tackle unexpected spills will prove useful, particularly if emergency services are required to administer further help to an employee who has suffered an accident, injury, or burn.
Displaying clear health and safety rules, accessible and from multiple touchpoints, will reinforce the need for proper maintenance and adherence to cleaning schedules, chemical handling, and hazard prevention. Conducting regular safety drills will also physically and mentally prepare personnel to follow the relevant steps if an accident or emergency ever arises.
There are clear standards outlined by the UK’s health and safety legislation like the Health and Safety at Work Act, COSHH regulations, and Genetically Modified Organisms regulations, among others. These provide frameworks to systematically identify and mitigate hazards via training, authorised work procedures, medical surveillance and robust record-keeping.
Working through hazard control measures is never one-and-done; it requires a willingness to learn, adapt, and be flexible as risks and hazards grow. Fostering a culture of open communication, consultation, and reporting of health risks and hazards in any facility as precarious as a laboratory will, ultimately, prove to be the best baseline safety measure to ensure its long-term stability and minimise risk exposure.