We are working towards an entirely new Wellbeing Management System and its integration in current business processes
Shapoorji Pallonji Bumi Armada Godavari Pvt Ltd (SPBAG) which operates and manages FPSO Armada Sterling V, located in east coast of India. Armada Sterling V is India’s largest FPSO for ONGC which has the world’s largest submersible turret production system. The FPSO is designed to operate in cyclonic conditions on the east coast of India. We spoke to Sudarshan Singh, HSSEQ & Compliance Head, SP Armada Oil Exploration Pvt. Ltd to understand more…
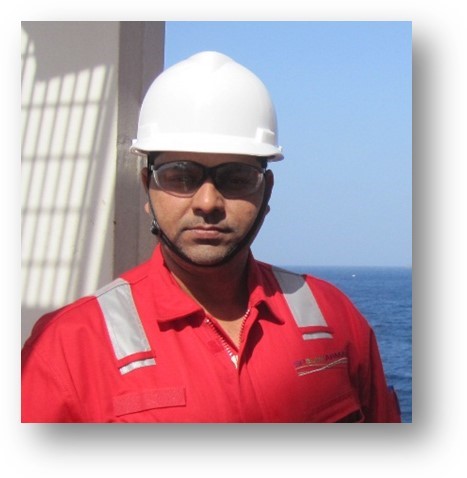
Interviewed by Adeesh Sharma & Nisha Biradar
1. Please tell us about your organization and its focus areas in HSE.
I am focussing on 3 companies which are owned, designed, built by us and currently operating and managing the three FPSOs in India providing Oil & Gas to the Nation ;
Shapoorji Pallonji Armada Oil And Gas Services Limited(SPAOGSPL) operates and maintains the FPSO ‘Armada Sterling’ located 200 Kms in high seas west coast of India.
SP Armada Oil Exploration Pvt Ltd (SPAOEPL) operates and maintains Armada Sterling II FPSO Site is located in the mid of Arabian Sea, approximately 210 Kms to the west of Mumbai, India.
Shapoorji Pallonji Bumi Armada Godavari Pvt Ltd (SPBAG) which operates and manages FPSO Armada Sterling V, located in east coast of India. Armada Sterling V is India’s largest FPSO for ONGC which has the world’s largest submersible turret production system. The FPSO is designed to operate in cyclonic conditions on the east coast of India.
FPSO is a floating production, storage and offloading facility, equipped with hydrocarbon processing equipment for separation and treatment of crude oil, produced water and associated gases, arriving on board from sub-sea oil wells via flexible pipelines.
20% of India’s crude oil production from Western offshore is by FPSO Armada Sterling and Armada Sterling II
Our FPSOs have huge storage capacity for the treated crude oil produced and is equipped with an offloading system to transfer the crude oil to shuttle tankers for shipment to refineries. FPSO Armada Sterling, Armada Sterling-II & Armada Sterling V primarily consists of Productions systems, Helideck, Accommodation, Engine & Machinery room, Pump Room, Subsea Systems–Risers, Turret & Mooring Systems, 7-MegawattX2 Turbine Generators, Marine Boilers, Life Saving appliances, Escape Systems & Cargo and Ballast Tanks etc.
The Organization has won various awards from OSH in past 2017, 2018, 2019 …..
We have achieved five Star ratings in British Safety Council and received the Sword of Honour for OHS & Process Safety and Globe of Honour Award from British Safety Council for Excellence in Environment Management and highlighting sensitivity towards environmental concerns and management.
FPSO operates 24X7, operations are managed by FPSO Offshore Installation Manager with the support of Crew and shore team in accordance with companies Integrated Management System to ensure safe operations and sufficient numbers of competent staff are available for designated job duties.
Our current focus areas in HSE are:
- Wellbeing – we have embarked on the journey to wellbeing in 2018 and 2024 IS SEEING enhanced focus to engage stakeholders on wellbeing and mental health, through British Safety Council best practices in wellbeing and mental health we aim to foster mind, body, and sense of purpose in individuals, teams, and our JVC Companies for a more resilient workforce and improved well-being in the workplace.
- Safety Case Review - All the risks are identified at a very early design stage of FPSO through various Formal Safety & Environmental studies & assessments. Risks are addressed during design and construction, the most significant risks \are documented in FPSO Safety Caseunder major accident event & its barriers are classified as Safety & Environmental Critical Element (SECE), we have planned to focus in 2024 & 2025 on Safety case engineering review through global SMEs.
- Performance Standards (PS) for Safety & Environment Critical Elements (SECEs) subject to external verification by an independent and competent person.
- Emergency Response Plan - Cyclones in the Indian coastal zones have been enhanced in frequency and magnitude due to climate change, as our employees and assets are positioned in east coast and west coast in high seas, there is a genuine concern about the increased destructive potential of tropical cyclones in the Indian subcontinent. Updating our Emergency Response Plan to make it more agile to cyclones and adverse weather, we holistically are focussing on review of engineering as well as command and control improvements in light increased adverse weather conditions.
- Adopting Technologies in Incident Management & Audit Management – work around “Synergi” software from DNV - Synergi Life software is designed to help organisations effectively manage enterprise risk, incidents, quality and operational excellence initiatives. Additionally, it offers a robust framework for seamless process and workflow rollout across the organisation for streamlined operations and increased efficiency.
- Adopting Best Technologies – American Bureo of Shipping(ABS) Digital platform for Innovations designed to tackle technical and regulatory challenges while operating more safely, securely and responsibly.
- Adopting best practices in Remote, Lone and Hybrid working, recently we have carried out a survey on same and incorporating the bast practice in our management system.
2. What challenges do you face as a key HSE professional?
The current challenges I am facing as a key HSE Professional include but are not limited to;
Stakeholder engagement especially on Mental Health & Wellbeing Issues – understanding the global best practices and implementation with Indian context, effective data collection, stakeholders’ engagement in spite of things looking positive it has been a big challenge getting 94% crew engagement, given their rotation cycle of 28 days on / 28 days off.
Changing/Evolving Regulations – Changing Regulations Due to recent issued OISD Standards as well DGS Circular’s Class changes, many of which are new & main intention is for ‘Safety of Life at Sea’ (examples placing immersion suits onboard, Mandatory ISM & MLC Compliance for MODU / SPS Vessels / Rigs / FPSO / Accommodation Barges, Risk Assessment for Crew Onboard endorsed by Flag etc. are some key points), HSE professionals are challenged to compliance and get the large amount of changes processed, huge amount of paperwork and get it complied with management of change process.
3. What strategies/solutions you deploy to alleviate those challenges?
The Strategies and solutions we have deployed to alleviate “Stakeholder engagement” including regulators like OISD, MoPNG and DGS
Establishing and implementing comprehensive integrated processes and strategic arrangements to engage different stakeholders under our “Integrated Management System framework, Communication & Consultation Procedure and Needs & Expectations Analysis, keeping it updated regularly through communication and consultation in line with Continual Improvement principal.
The arrangement and key strategy deployed are:
- Identifying stakeholders: Identifying “interested parties” (stakeholders) who receive our services & products, or who may be impacted by them, or those parties who may otherwise have a significant interest in our company. These parties are identified in the document Interested Parties Needs & Expectation’s relevant to COTO & Risk (COTO & PESTLE), Communication & Consultation Procedure; MUM-GEN-IMS-GDL-0001 and IMS Manual MUM-GEN-IMS-MAN-0001. The stakeholders are categorized as Internal(workers including non managerial works, contract employees, etc and external
- Stakeholder mapping: The interested parties and their needs and expectations are mapped, recorded, analysed, monitored and reviewed on a recorded schedule. Stakeholders are categorised based on their influence and interest.
- Understand their needs and expectations: Get to know their expectations for outcomes and strategic planning thru;
- Tailored communication & consultation: Communication and Consultation Procedure developed and fully implemented to actively & effectively communicate, engage & consult stakeholders ensuring they are part of decision making as relevant.
- Engagement through Regular updates and two-way feedback: Keep stakeholders informed and involved, examples of such engagement arrangements established for different stakeholders are cited below;
- Internal
- Health, Safety, Security, Environmental Sustainability and Quality (HSSEQ) Policies, OHSMS(IMS), Core values, review of objectives and targets, HSSEQ Lessons learnt, HSSEQ Issues are regularly communicated to employees, contractors, Joint venture company stakeholders, business partners etc, during employment, award of contracts, interactions forums, consultation is done during update of versions, before new release. These are also openly discussed and feedback is sought from crew, contractor, 3rd party present during weekly and monthly HSSEQ meetings, monthly HSEW(Safety) Committee meetings; as a fixed agenda, the outcomes and any actions generating from such forums are minuted and actions are entered in installation action tracker, followed up for effective implementation. Consultation and communication with other stakeholders are also done through emails, letter, displays, communication board, induction and HSE Passport trainings.
- HSSEQ Reports, Newsletter, Safety Alerts, Health & wellbeing mailers through email
- Weekly Emergency Response Exercise
- Safety Observation Program – Daily
- Life Saving Rules - Daily
- Safety Leadership Walkaround – Weekly
- Toolbox talks - Daily
- External examples include
- Incident / Near Miss Reports to business partners, as well as to Director General of Shipping, Oil Industrial Safety Directorate through client
- Monthly reports to client
- HSSEQ related information quarterly / annually to stakeholders – board of directors / business partners
- HSE & wellbeing information to stakeholders via ESG disclosure
- HSE Passport, competence and external training report to management/JV Company/Stakeholders
- Daily communications with Navy and Headquarter Defence Advisory Group
Corporate Health, Safety, Environmental Sustainability and wellbeing communication, participation & consultation channels/approach/tools include;
- HSSEQ Video Channels /monthly / Utilizing Corporate social media to communicate HSSEQ related matters/ Communication/Participation
- HSSEQ Review Meeting / Monthly / Annual / Review presentation on Progress of Planned HSSEQ Objectives & Targets // Communication Participation Consultation
- Utilizing Corporate social media to communicate HSSEQ related matters across SPBA / Monthly / HR /Communication
- OHSMS(IMS) / Frequent/As and when necessary/ IMS with latest HSSEQ information/Document Controller
- Presidents Message on HSSEQ/Annually / Sharing of Leadership commitment and directions in HSSEQ via email or Video conference / Communication
- SPBA JVC partners / Updated as and when necessary / Sharing the HSSEQ information to the public / Communication
The organization has implemented the BSC five-star audit recommendations as part of its Continual Improvement, by engaging all stakeholders in its recent survey completed on 24th July, communicating with all onboard installation, those who are in their off-duty period including all the office staff. The employee’s engagement response rate has been upto 94%.
We are further reviewing our annual performance objectives for stakeholder engagements, KPIs, Targets to enhance its
Continual Improvement is at the core of company OH&SMS system and involves a never-ending efforts to expose and eliminate root causes of problems and to achieve better all-round understanding, performance and desired outcomes. The approach involves all stakeholders in evaluating and incrementally improving on an ongoing basis, all factors related to organizations OH&S management and performance thru IMS PDCA Cycle.
I would quote Some important buying for larger benefits drawn,
- British Safety Council recommendation offered us lens to enhanced understanding of our stakeholder engagement dynamics
- Onboard crew engagement program has helped to keep the crew motivated, alert, aware of hazards and accident free. An example is due to various HSE Engagement program specifically Life Saving Rules interactions, stop work authority intervention and Safety observation program, the overall safe behaviour of crew members including contractors and every stakeholder on installation has improved not only at FPSO but at their homes/in their personal life also.
- Our transparent communication and consultation has contributed to enhance organizational transparency, which has lead to an environment where crew, contractors, class, flag, regulator and client ONGC as well as BSC trust that relevant information is shared proactively. Beyond instilling trust, this openness layed the foundation for a culture of accountability and integrity, indispensable for effective risk management. We are able to better identify, assess, and proactively address risks by establishing this culture where information is communicated openly as per established procedure.
An example of benefits recent engagement through survey has increased awareness levels, understanding of the OHS requirements and their needs and expectations.
Occupational Health Management Plan (OHMP) – training and campaigns on health and wellbeing has helped employees manage their health better, both mental and physical. Also they have gained knowledge on various diseases and health issues(such as malaria, hepatitis, cancer) including its prevention, which are helpful to them, their families and friends. After onboard sessions many of our crew members have taken hepatitis A & B and typhoid vaccination and also done for their kids. Most of the crew members have quit smoking after repeated engagement sessions and awareness programs on “cancer” and “ill effects of smoking” as per OHMP Wellbeing Calendar.
Benefits encompass informed decision-making, enhanced transparency, improved risk management, and strengthened stakeholder relationships. Barriers, such as technical jargon and resistance to change, are addressed to optimize communication effectiveness. The conclusion underscores the pivotal role of communication & consultation, and recommendations provide a roadmap for organizations to navigate complexities and maximize the impact of Five Star audit findings on organizational resilience and strategic decision-making.
Lastly, the positive outcomes of effective engagement include strengthened relationships with stakeholders. Whether they are employees, managers, contractors, business partners, Class, Flag, or regulatory bodies, engaged and well-informed stakeholders has contributed to a collaborative organizational culture. This collaborative spirit fosters us better cooperation, shared responsibility, and a collective commitment to addressing OH&S risks, issues, audit findings, etc, reinforcing the organization's resilience in the face of evolving Occupational Health, Safety and Wellbeing challenges.
4. What are your views on current HSE scenario in Indian industries and what more needs to be done to change it?
The HSEW scenario in our country is very complex. We are one of the fastest growing nations in the world, but on the other hand nonadherence to health safety and well-being standards, rules and regulations is still leading to accidents / incidents in most of the industries in India. The consequences are frequently seen in the form of fire & explosions, fatalities, injuries and diseases to personnel.
Unprecedented growth and progress go hand in hand with challenges such as culture diversity, huge workforce, lack of training, education, unorganized sectors, low wage, availability of cheap labor, meagre public spending on health, inadequate implementation of existing legislation, lack of reliable HSEW data, shortage of HSEW professionals, multiplicity of statutory controls, apathy of stakeholders and infrastructure problems.
Some industries are a step ahead with focus on occupational health safety and wellbeing, but it is not uniform or not even close when speak about the overall safety in Indian industries. Many industries, organization leaders talk about safety is priority, but still it gets diluted when comes to profit, business targets etc.
What more needs to be done;
- Underreporting of industrial injuries is serious issue especially in construction, unorganised sectors, medium scale and small scale industries.
- A lot of focus and collective effort is required to ensure a safe working environment is provided to employees of various industries across country.
- Developing and maintaining an effective safety culture in the industry / organisation should be one of the focus area. Organization should focus to embed safety as a core value and integrate in every aspects of work.
- The existing labor laws, policies, inspection system for medium and small scale industries need to be revisited by the government.
- Complying with the safety rules and regulations - strict actions need to be taken to prevent violations and deviations from the legal requirements.
- Public Awareness for preventing accidents (whether it be work related or public safety like road Safety) and diseases need to be encouraged throughout the nation.
- Developing a HSEW Mindset and HSEW Culture with with Country perspective is the need of the Hour;
WAY FORWARD
Institutions like Informa Markets, British Safety Council in association with Industry Torchbearers & HSEW Professionals could assist and bring a positive outcome on the above issues.
Including Core Values for seeding in schools’ colleges universities, and comprehensive HSEW training program in industries will support to proactively minimize the risk of injuries, illness and accidents. Looking at the diversity & vastness if HSE issues we propose Government to consider separate ministry for HSEW who can focus on HSEW Industry Issues and Integrate various HSEW implementation bodies such as OISD, DGFASLI, DGMS, CPCB etc. to have more focussed and united approach.
Government of India, under the Leadership of honourable Prime minister Shree Narendra Modiji stands committed to review & improve the National Policy on Safety, Health and Environment at Workplace and legislations through tripartite consultation, improve enforcement, compilation and analysis of statistics; develop special programmes for hazardous operations and other focus sectors, set up training mechanisms, create nation-wide awareness, arrange for the mobilisation of available resources and expertise. This commitment gives high hope and expectation to see India as a place where the workers can expect a safe place to work and maintain a healthy mental and physical wellbeing. The Future for Improving Health, Safety, Environmental Sustainability, ESG, Wellbeing, Asset Integrity is VERY BRIGHT that will provide industry a cohesive sustainability under the guidance of Industry Torch bearers, HSEW Professionals and will be the upcoming VOICE of people.
5. What new HSE initiatives are you planning to implement within your organization in the near future?
Few of the New HSE Initiatives in near future ;
Wellbeing - Working towards an entirely new Wellbeing Management Systems and its integration in current business Process. Adoption of best practice and technologies to enhance employee’s mental health and wellbeing. We also plan to go for benchmarking Wellbeing & Mental Health against Global best practice.
Engagement with OEUK - engage with industry specialists, foster valuable HSE & Wellbeing Insights through networking, and explore potential improvement opportunities.
Digitalization “Synergi Life” software from DNV - Synergi Life software is designed to help organisations effectively manage enterprise risk, incidents, quality and operational excellence initiatives. Additionally, it offers a robust framework for seamless process and workflow rollout across the organisation for streamlined operations and increased efficiency.
Modernising IMS Document Management for efficiency through AGTIV EDCS
Recovery of LP separator gas for utilization as fuel gas by installing booster compressor at FPSO Armada Sterling, this will reduce Marine Diesel Oil consumption. The current fuel gas for GTGs / Boilers is insufficient because related gas from the reservoir is decreasing, and the boilers occasionally run on diesel. As the gas from the LP Separator is now flared, the intention is to use it as an extra fuel gas supply to the boilers and GTGs. Carbon footprints can also be estimated via diesel use, assuming use of 12 KL per day, the overall carbon footprint would be around 31.68 Tons per day.